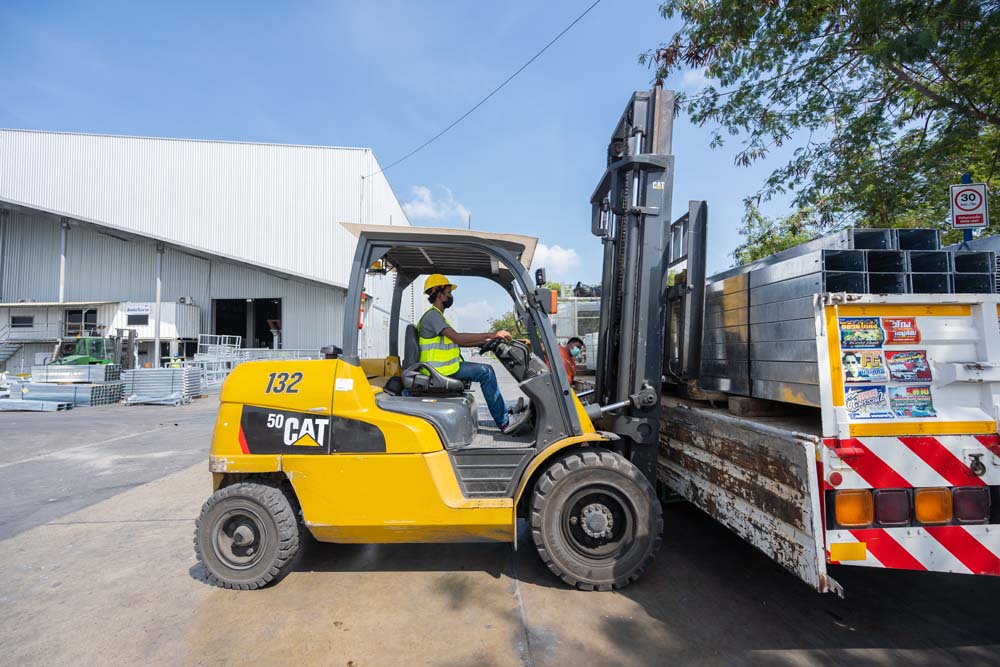
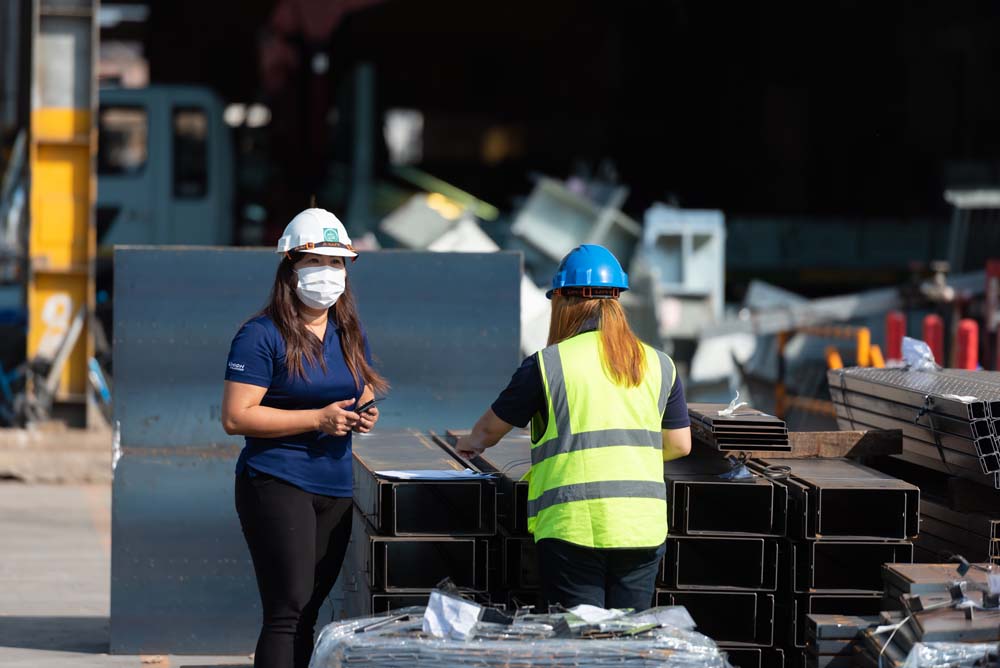
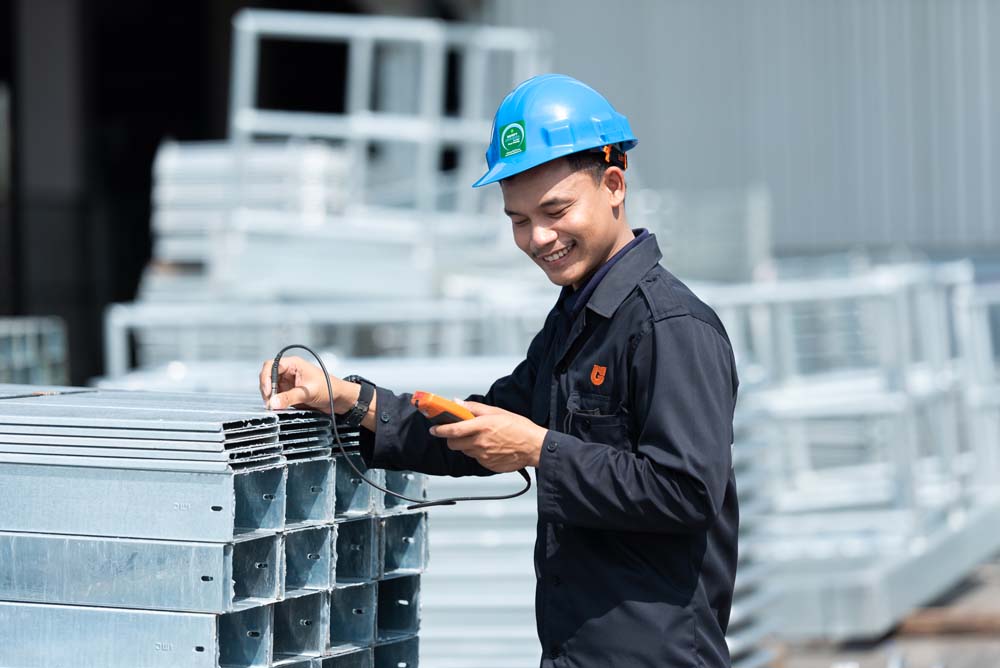
Hot dip galvanized
Hot-dip galvanizing service
At Union Galvanizer Limited, we are dedicated to providing the highest quality hot-dip galvanizing services to meet the needs of customers across various industries. With extensive experience and expertise, we have developed modern techniques and processes. We approach every service with sincerity, ensuring that your products are durable and have a long lifespan.
- Zinc Special High Grade 99.995%
We use only the best materials, including Zinc Special high grade, to ensure that your products receive the highest level of protection against corrosion and rust. Our Zinc Special high grade material is carefully selected for its purity and consistency, and undergoes rigorous quality testing to ensure that it meets our high standards. With our commitment to quality and attention to detail,
you can trust that your products will be protected for years to come. - Quality inspection of customer’s products (black steel)
We conduct thorough quality checks on customer’s black steel products before they undergo the galvanization process. This meticulous inspection ensures that the products are accurate, complete, and meet all standards. This ensures that they proceed to the next stages with high quality and efficiency, overseen by experienced and skilled technicians.
- JIGING AND SURFACE PREPARATION
Jigging is the process of suspending or holding the steel or iron product during the galvanizing process. The proper jigging of products is essential to ensure that the zinc coating is evenly applied to all areas of the product, including corners, edges, and recesses. Poor jigging can lead to areas of the product not being properly coated, which can result in the formation of bare spots and reduced protection against corrosion and rust. Surface preparation involves cleaning and preparing the metal surface to ensure optimal adhesion of the zinc coating. This is done by removing any rust, oil, or other contaminants that may be present on the surface. Proper surface preparation is essential to ensure that the zinc coating adheres properly to the surface and provides effective corrosion protection. Failure to properly prepare the surface can result in the zinc coating flaking or peeling off, which can compromise the overall protection of the metal.
- GALVANIZING AND QUENCHING
Galvanizing: The products are then immersed in a bath of molten zinc. The zinc reacts with the surface of the metal to form a protective layer that bonds to the surface. The temperature of the zinc bath is typically around 450-460C. Quenching: The product is then removed from the bath and allowed to cool in air or by immersion in water.
- INSPECTION
Visual Inspection: The products are visually inspected for any defects or issues such as bare spots, drips, or other imperfections. Coating Thickness Measurement: The thickness of the zinc coating is measured at several locations on the product using a magnetic thickness gauge. The minimum coating thickness required varies depending on the application and the standard or specification being followed. Adhesion Testing: Adhesion tests are performed on the zinc coating to ensure it adheres to the metal surface. This can be done through a variety of methods, including bend tests or knife tests.
- GRINDING AND TOUCH-UP
Grinding: During the hot dip galvanizing process, some areas of the metal may experience excess zinc buildup or other imperfections that need to be smoothed out. Grinding is the process of removing any excess zinc or other defects on the surface of the product. This is typically done using power tools such as grinders or sanders.
Touch-up : Touch-up with zinc-rich paint: After the grinding process, any areas of bare metal exposed during grinding can be touched up with zinc-rich paint. Zinc-rich paint contains high levels of zinc, which provides a sacrificial layer of protection against corrosion. This touch-up process helps ensure that the entire surface of the product is adequately protected against corrosion. - Final inspection and transportation
Our experienced team conducts a comprehensive inspection of all of our products to ensure that they meet the required specifications and are free from any defects or imperfections. We use advanced equipment and technology to carry out these inspections, and our team is trained to identify any potential issues that may impact product quality. Once our final inspection is complete and our products have been approved, we are ready to deliver them to our customers. Our delivery process is designed to be efficient and reliable, with a focus on ensuring that our products are delivered on time and in excellent condition.